How to Choose a Safety Relay: Dadisick's Ultimate Guide
Understanding Safety Standards
ISO 13849-1
Risk Level | PL Rating |
Low | PLa/PLb |
Medium | PLc |
High | PLd |
Very High | PLe |
IEC 62061
Safety Integrity Level (SIL) | Probability of Dangerous Failure on Demand (PFDavg) | Probability of Dangerous Failure per Hour (PFH) |
SIL 1 | ≥ 10⁻² to < 10⁻¹ | ≥ 10⁻⁸ to < 10⁻⁷ |
SIL 2 | ≥ 10⁻³ to < 10⁻² | ≥ 10⁻⁸ to < 10⁻⁷ |
SIL 3 | ≥ 10⁻⁴ to < 10⁻³ | ≥ 10⁻⁷ to < 10⁻⁶ |
SIL 4 | ≥ 10⁻⁵ to < 10⁻⁴ | ≥ 10⁻⁶ to < 10⁻⁵ |
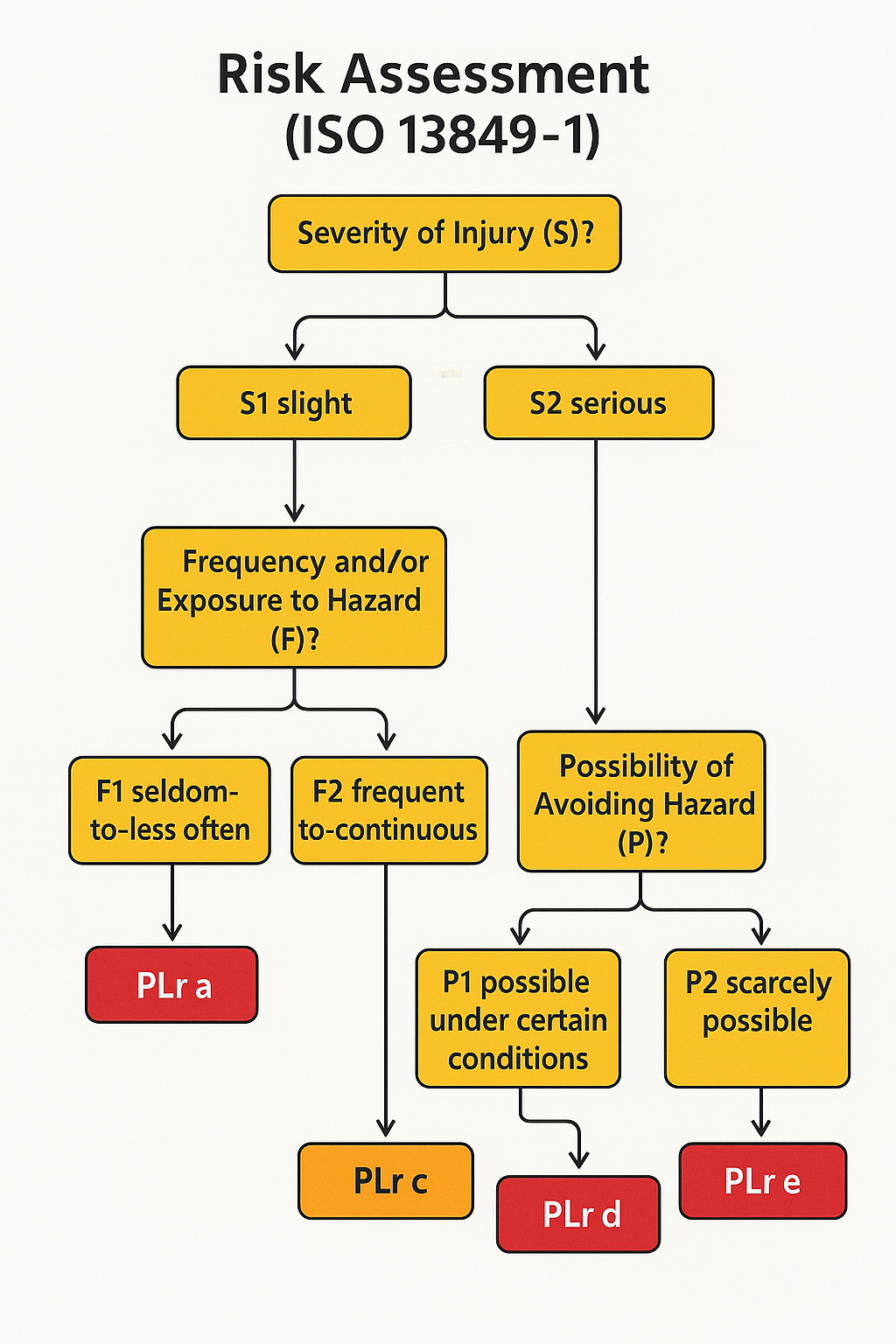
Step 1: Conduct a Risk Assessment
Step 2: Determine the Safety Functions
Step 3: Select the Appropriate Safety Relay
Selection Criteria | Description | |
PLr Compliance | Ensure the relay meets or exceeds the required Performance Level (PLa to PLe). | |
Input Types | Match the relay to input devices, such as E-stop buttons or safety switches. | |
Number of Channels | Choose single, dual, or triple channels based on redundancy needs. | |
Reset Mode | Select manual, automatic, or monitored reset depending on the application. | |
Response Time | Ensure the relay’s response time meets the hazard’s stopping time requirements. | |
Diagnostic Features | Opt for relays with fault detection and LED indicators for easier maintenance. | |
Expandability | Consider if the relay supports additional safety inputs or network integration. |
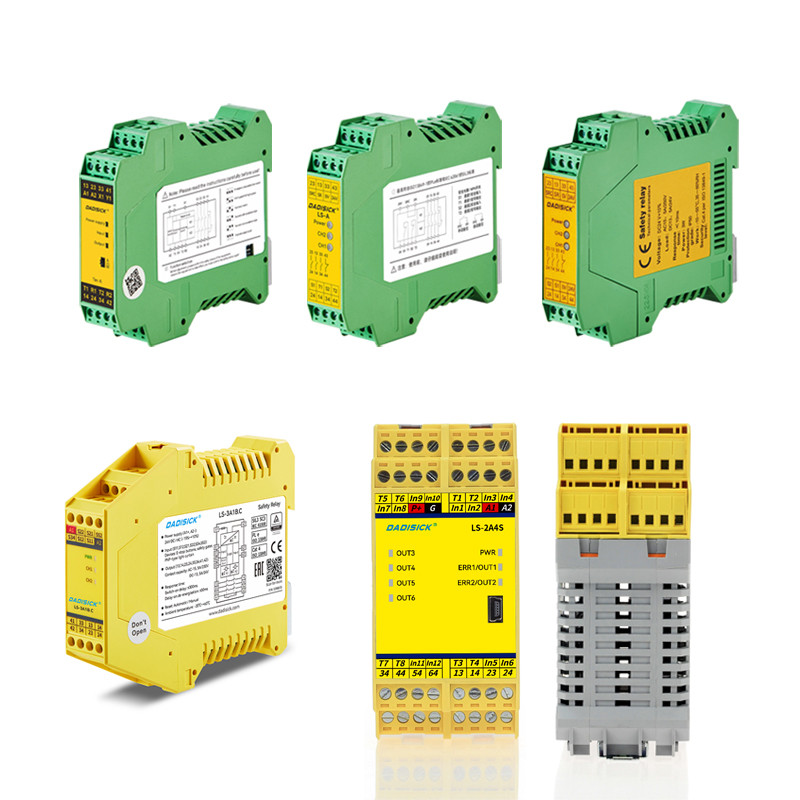
Step 4: Configuration and Wiring
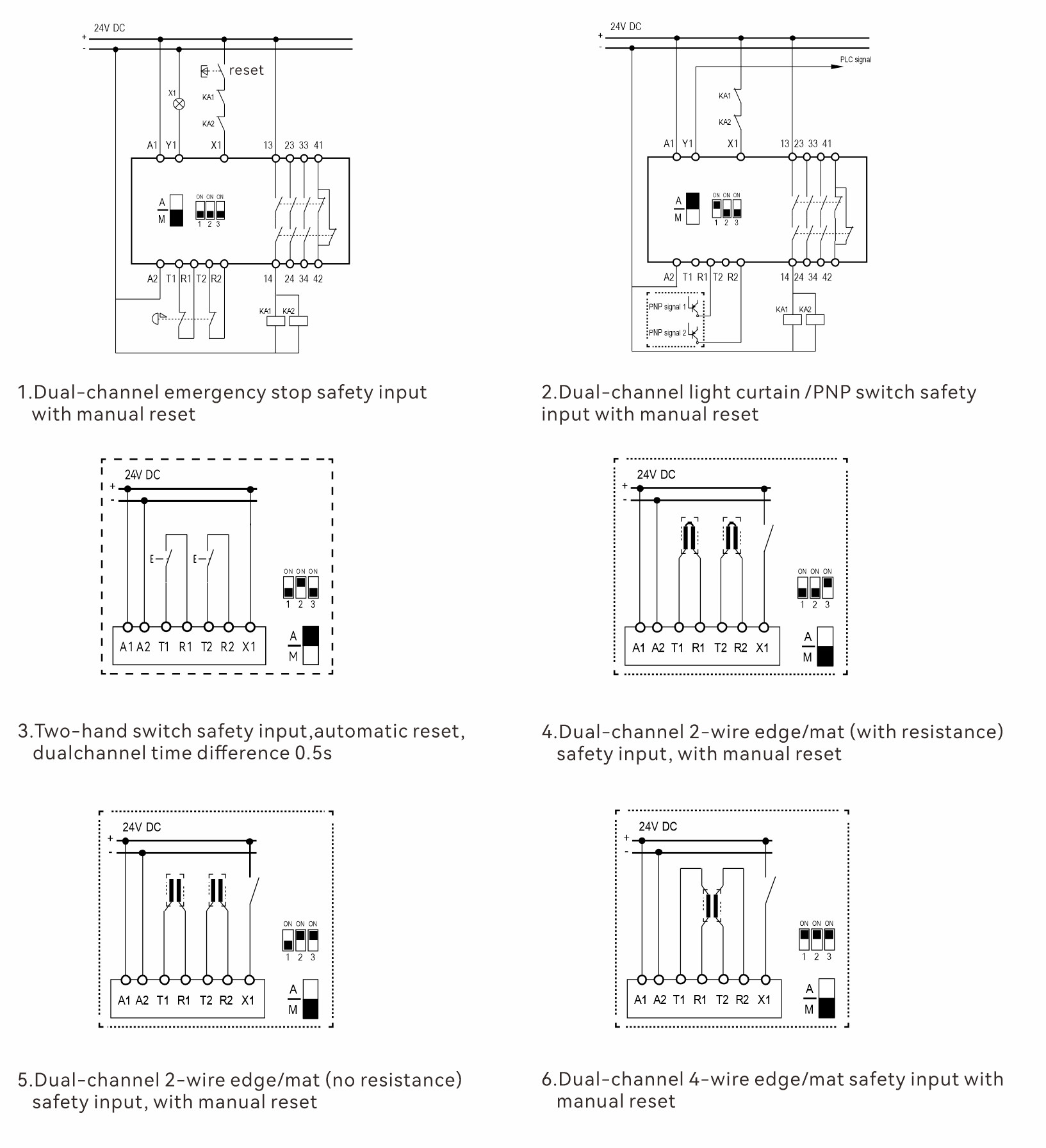
Step 5: Validation and Testing
Model | Key Features | Applications | |
Multifunctional, auto/manual reset, DIP switch configuration, high-safety monitoring | Complex industrial systems | ||
Economical, dual-channel design, easy integration | Automated production lines, robotic systems | ||
3 NO + 1 NC contacts, for emergency stops and safety gates | Cost-sensitive applications | ||
Configurable, 6 Redundant channels of safety inputs, multiple outputs | Complex safety systems | ||
Cat.4 compliant, supports multiple safety functions | High-risk industrial environments |
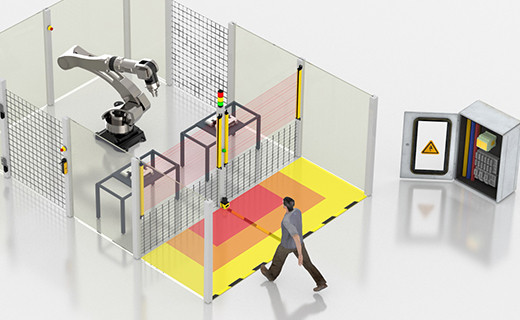